How WMS Optimizes Inventory Control and Reduces Costs
Effective inventory control is a cornerstone of successful warehouse management. In today’s competitive business landscape, the ability to maintain optimal inventory levels while minimizing costs is crucial. Implementing a Warehouse Management System (WMS) can significantly enhance inventory control and drive cost savings. In this blog post, we’ll explore how a WMS achieves these goals and how it can help streamline your inventory management.
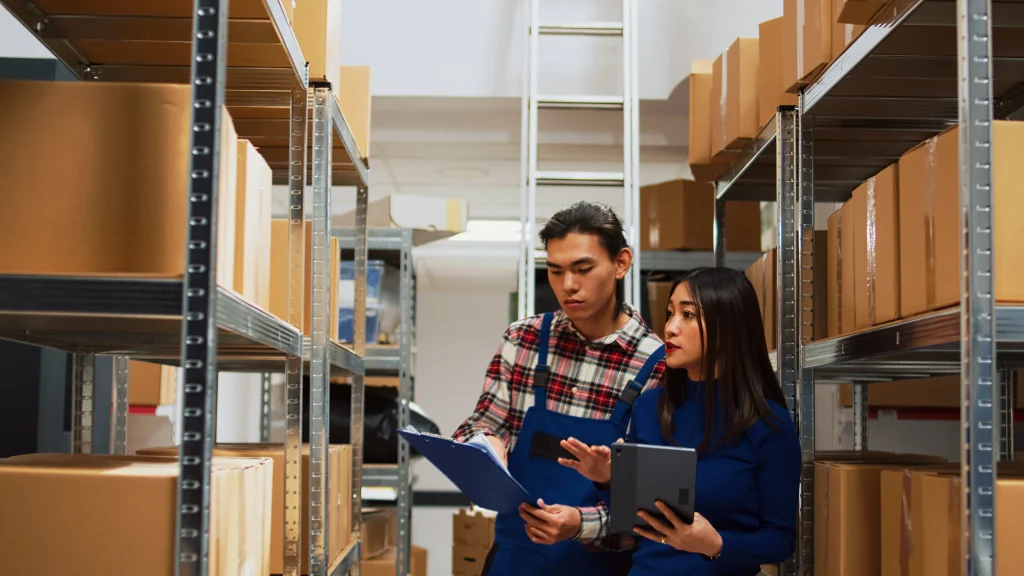
Understanding Inventory Control
Inventory control involves managing stock levels to meet customer demand without overstocking or understocking. Poor inventory control can lead to excess holding costs, stockouts, and lost sales. A WMS provides the tools and insights needed to optimize inventory control and reduce associated costs.
Real-Time Inventory Visibility
One of the key benefits of a WMS is real-time visibility into inventory levels. Traditional inventory management methods often rely on periodic stock counts and manual data entry, which can lead to inaccuracies and delays.
- Accurate Stock Levels: A WMS uses barcode scanning to update inventory levels in real-time, ensuring accurate stock records.
- Instant Updates: With real-time data, warehouse managers can make informed decisions quickly, such as reallocating stock or adjusting reorder points.
- Reduced Errors: Automation reduces the risk of human error in inventory tracking, leading to more reliable data.
Real-time visibility allows you to respond swiftly to changes in demand and maintain optimal stock levels, reducing the costs associated with excess inventory and stockouts.
Demand Forecasting
Effective inventory control relies on accurate demand forecasting. A WMS leverages historical data and advanced algorithms to predict future inventory needs.
- Historical Data Analysis: It analyzes past sales data to identify trends and seasonal fluctuations, helping you anticipate demand.
- Predictive Analytics: The system uses predictive analytics to forecast future demand, allowing you to adjust inventory levels proactively.
- Optimized Stock Levels: By understanding demand patterns, you can maintain the right amount of stock to meet customer needs without overstocking.
Accurate demand forecasting helps reduce the costs associated with overstocking, such as storage fees and obsolescence, while ensuring that you have enough inventory to meet customer demand.
Streamlined Replenishment
A WMS streamlines the replenishment process, ensuring that stock levels are maintained without unnecessary delays.
- Clear Replenishment Signals: It provides clear signals and alerts when inventory levels are low, prompting timely replenishment actions by warehouse staff.
- Efficient Inventory Transfers: The system facilitates efficient transfers of inventory between different locations or zones within the warehouse, ensuring stock is available where itβs needed most.
- Manual Checklists: It supports the use of manual checklists to guide warehouse staff through the replenishment process, ensuring no steps are missed and replenishments are conducted promptly.
Streamlined replenishment processes ensure that inventory is always available when needed, reducing the risk of stockouts and associated costs.
Enhanced Inventory Accuracy
Inventory inaccuracies can lead to costly mistakes, such as stockouts or overstocking. A WMS improves inventory accuracy through automation and real-time data updates.
- Cycle Counting: Regular cycle counting allows you to verify inventory levels without the need for full physical counts.
- Error Reduction: By automating data entry and inventory tracking, a WMS minimizes the risk of human error.
- Discrepancy Management: The system identifies discrepancies between recorded and actual stock levels, allowing you to investigate and resolve issues promptly.
Enhanced inventory accuracy leads to better decision-making and reduces the costs associated with inventory discrepancies.
Cost Savings
Implementing a WMS can lead to significant cost savings in various aspects of warehouse operations.
- Labor Efficiency: Automation reduces the need for manual labor, allowing you to allocate resources more efficiently.
- Storage Costs: Optimized inventory levels reduce the amount of space needed for storage, lowering warehousing costs.
- Reduced Waste: Improved inventory accuracy and demand forecasting help reduce waste due to overstocking and obsolescence.
With a warehouse management system, you can achieve these cost savings while maintaining high levels of customer satisfaction and operational efficiency.
Conclusion
In summary, a Warehouse Management System like 8Stock offers numerous benefits for inventory control and cost reduction. By providing real-time visibility, accurate demand forecasting, streamlined replenishment, and enhanced inventory accuracy, 8Stock helps businesses maintain optimal stock levels and minimize costs. Investing in a WMS is a strategic decision that can drive significant improvements in your warehouse operations and contribute to long-term business success.
Discover how 8Stock can optimize your inventory control and reduce costs. Contact us today for a demo and see the difference a top-tier WMS can make for your business.