To manage warehouse labor efficiently is crucial for ensuring smooth operations, minimizing costs, and maximizing productivity. Whether you’re running a small business or a large-scale distribution center, how you manage your workforce can make or break your operations. In this post, we’ll explore some effective strategies for managing warehouse labor, complete with real-life examples that can help you streamline your processes and keep your team motivated.
Manage Warehouse Labor 1. Proper Workforce Planning
Effective labor management starts with proper workforce planning. This involves determining the right number of workers needed at any given time, based on the demand for goods and the workload in the warehouse.
Example: Imagine a warehouse that processes orders for an online retailer. During peak shopping seasons like Black Friday or year-end sales, the demand skyrockets. In this scenario, it’s essential to increase the number of temporary workers to handle the surge in orders. On the other hand, during off-peak seasons, the workforce can be reduced to cut down on unnecessary labor costs. Planning ahead and adjusting the workforce based on demand can help in maintaining efficiency without overworking your staff.
Tip: Use historical data to forecast busy periods and plan your workforce accordingly. This not only helps in avoiding last-minute scrambles but also ensures that your team is not underutilized during slower periods.
Manage Warehouse Labor 2. Cross-Training Employees
Cross-training involves teaching employees how to perform tasks outside of their usual responsibilities. This strategy ensures that workers can fill in for one another during absences or peak times, providing flexibility and reducing bottlenecks.
Example: In a warehouse that handles both inbound and outbound operations, you might have separate teams for receiving goods and shipping them out. By cross-training your receiving team to handle outbound shipments, you create a more versatile workforce. If a sudden influx of orders overwhelms the shipping team, the receiving team can step in to assist, ensuring orders go out on time.
Tip: Implement a rotation program where employees spend a few hours each week working in different departments. This will not only make them more skilled but also foster a greater understanding of the overall operation.
Manage Warehouse Labor 3. Implementing Technology Solutions
Technology can significantly enhance labor management by automating tasks, tracking performance, and optimizing workflows. Warehouse Management Systems (WMS) like 8Stock are powerful tools that can help managers monitor employee productivity, allocate tasks efficiently, and reduce manual errors.
Example: A large warehouse might use a WMS to assign picking tasks to workers based on their proximity to the items. This minimizes the time workers spend walking and maximizes their picking efficiency. The system can also track how long it takes to complete tasks, allowing managers to identify areas where additional training might be needed.
Tip: Invest in a WMS that suits your warehouse size and needs. Start with basic features like task tracking and gradually incorporate more advanced options like automation and real-time analytics.
Manage Warehouse Labor 4. Incentive Programs
Creating incentive programs is a great way to motivate employees and increase productivity. These programs can be based on performance metrics such as the number of orders picked, the accuracy of order fulfillment, or the speed of task completion.
Example: A warehouse could implement a monthly bonus system where employees who consistently meet or exceed their targets receive a cash bonus or other perks like extra paid time off. For instance, if a worker maintains a 99% accuracy rate in picking orders, they could receive a bonus at the end of the month. This not only boosts morale but also encourages healthy competition among employees.
Tip: When designing incentive programs, make sure they are fair and achievable. Set clear goals and communicate them effectively to your team. Regularly review and adjust the targets to keep the program relevant and motivating.
Manage Warehouse Labor 5. Regular Training and Development
Continuous training is key to maintaining an efficient workforce. Regular training sessions help employees stay updated on the latest industry practices, safety protocols, and the use of new technologies.
Example: A warehouse that introduces a new automated picking system should provide comprehensive training to all employees on how to use it effectively. Without proper training, the new system could lead to confusion and decreased productivity. Regular refresher courses on safety procedures can also reduce the risk of accidents, ensuring a safer working environment.
Tip: Schedule regular training sessions, both for new hires and existing staff. Incorporate a mix of classroom-style learning and hands-on practice to cater to different learning styles. Additionally, consider offering opportunities for career development, such as leadership training for those interested in supervisory roles.
Manage Warehouse Labor 6. Efficient Communication Channels
Clear and efficient communication is crucial in a fast-paced warehouse environment. Miscommunication can lead to errors, delays, and frustration among employees. Implementing robust communication channels can help in disseminating information quickly and accurately.
Example: In a large warehouse, a manager might use a mobile communication app to send instant updates to the entire team. For instance, if there’s a sudden change in the order priority, the manager can immediately notify all relevant employees through the app, ensuring everyone is on the same page.
Tip: Consider using a mix of communication tools, such as intercom systems, mobile apps, and regular team meetings. Ensure that communication is a two-way street, where employees feel comfortable voicing their concerns or suggestions.
Manage Warehouse Labor 7. Maintaining a Positive Work Environment
A positive work environment is essential for employee satisfaction and retention. This includes everything from maintaining clean and safe working conditions to fostering a culture of respect and teamwork.
Example: A warehouse that actively promotes teamwork might organize regular team-building activities, such as group lunches or off-site outings. When employees feel valued and part of a team, they are more likely to stay engaged and committed to their work.
Tip: Regularly solicit feedback from employees on how to improve the work environment. Implementing small changes, like improving break room facilities or recognizing employee achievements, can go a long way in maintaining a positive atmosphere.
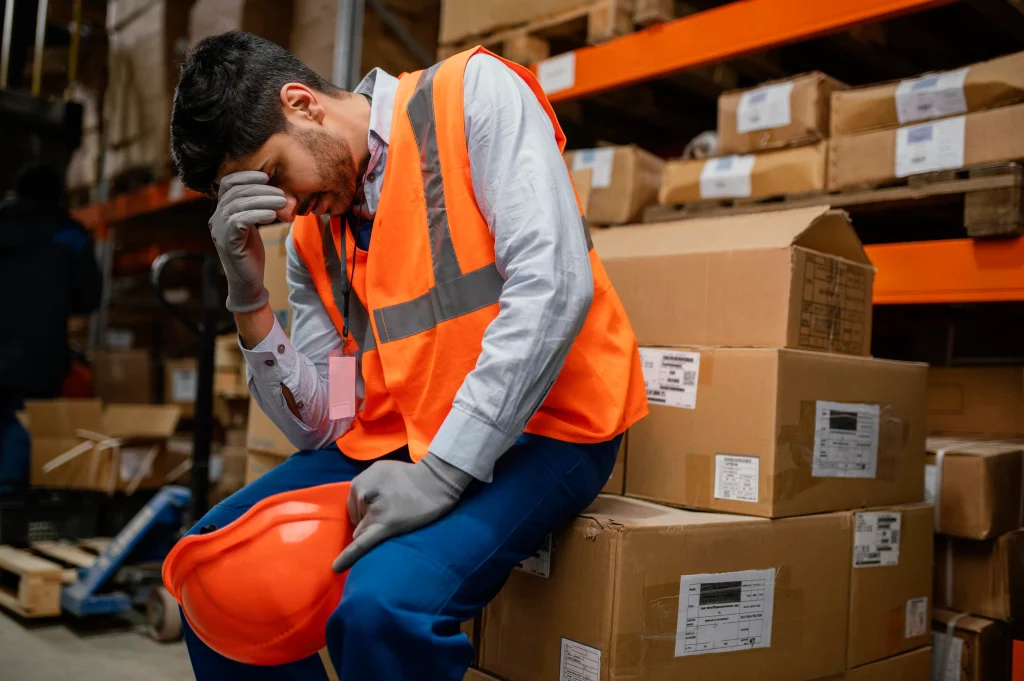
Manage Warehouse Labor 8. Optimizing Shift Schedules
Warehouse operations often run 24/7, requiring careful management of shift schedules to avoid worker fatigue and burnout. Optimizing shift schedules can help in balancing workloads and ensuring that workers are not overburdened.
Example: A warehouse that operates around the clock might implement a rotating shift schedule, where employees alternate between day and night shifts. This prevents any one group from consistently working the less desirable night shifts and helps in distributing the workload more evenly.
Tip: When creating shift schedules, consider factors like employee preferences, workload distribution, and legal requirements regarding working hours and breaks. Use scheduling software to automate the process and avoid conflicts or overlaps.
Manage Warehouse Labor 9. Employee Engagement and Recognition
Engaged employees are more productive, and recognizing their efforts can lead to higher job satisfaction and retention rates. Regularly acknowledging the hard work of your employees fosters a sense of pride and loyalty within the team.
Example: A warehouse might implement an “Employee of the Month” program where outstanding workers are recognized publicly and rewarded with a certificate, a small bonus, or a preferred parking spot. Such initiatives show employees that their contributions are valued and appreciated.
Tip: Make recognition a regular part of your management practices. Even small gestures, like a simple thank you note or public acknowledgment during team meetings, can have a significant impact on employee morale.
Manage Warehouse Labor 10. Monitoring and Continuous Improvement
Effective labor management is an ongoing process that requires regular monitoring and adjustments. By continuously analyzing performance metrics and seeking feedback, you can identify areas for improvement and make necessary changes.
Example: A warehouse manager might notice a recurring issue with order picking errors during the late-night shift. Upon investigating, they discover that workers are experiencing fatigue due to long hours. To address this, the manager could adjust the shift length or provide additional breaks during the night shift to improve accuracy and reduce errors.
Tip: Use data analytics to monitor key performance indicators (KPIs) such as productivity, accuracy, and employee satisfaction. Regularly review these metrics and involve your team in brainstorming solutions to any issues that arise.
Conclusion
Managing warehouse labor effectively requires a combination of strategic planning, technology, and a focus on employee well-being. By implementing the strategies outlined above, you can create a more efficient and motivated workforce, leading to smoother operations and better overall performance. Remember, your employees are your greatest asset, and investing in their development and satisfaction will pay off in the long run.
Whether you’re using a Warehouse Management System like 8Stock, click here to request for a demo, to streamline tasks or implementing incentive programs to boost productivity, the key is to remain flexible and responsive to the needs of both your business and your workforce. With the right approach, you can turn labor management from a challenge into a strength that drives your warehouse’s success.