Top 10 Common Inventory Management Problems and How to Solve Them
Inventory management is crucial for any business. It ensures that products are available when customers need them, and it keeps costs down by preventing overstocking or stockouts. However, many businesses, especially small and medium enterprises (SMEs), face common inventory management problems. Here are the top 10 issues and how to solve them.
1. Inaccurate Inventory Records
Problem:
Inaccurate inventory records can lead to stockouts, overstocking, and lost sales. This often happens due to manual errors, lack of proper tracking, or outdated systems.
Solution:
- Implement a Warehouse Management System (WMS):
Systems like 8stock can automate inventory tracking and reduce human errors. - Regular Audits:
Conduct regular physical inventory audits to verify the accuracy of your records. - Train Staff:
Ensure your team knows how to use the inventory system correctly.
2. Overstocking
Problem:
Overstocking ties up capital and increases storage costs. It can also lead to obsolete inventory.
Solution:
- Use Demand Forecasting:
Predict future sales based on historical data to maintain optimal stock levels. - ABC Analysis:
Categorize inventory into three groups (A, B, C) based on importance and prioritize management efforts on high-value items. - Set Reorder Points:
Define when to reorder based on lead time and average sales.
3. Stockouts
Problem:
Stockouts result in missed sales opportunities and unhappy customers. This often happens due to poor forecasting or delayed supplier shipments.
Solution:
- Safety Stock:
Maintain a buffer stock to cover unexpected demand spikes or supplier delays. - Reliable Suppliers:
Build relationships with dependable suppliers to ensure timely deliveries. - Real-time Tracking:
Use inventory management software to monitor stock levels in real-time.
4. Inefficient Warehouse Layout
Problem:
An inefficient warehouse layout can cause delays in picking and shipping, leading to longer lead times and higher labor costs.
Solution:
- Optimize Layout:
Design your warehouse layout to minimize travel time for pickers. Place high-demand items near packing areas. - Use Labels and Signage:
Clear labels and signs can help staff find items quickly. - Regularly Review Layout:
Adapt the layout based on changing inventory needs and seasonal demands.
5. Lack of Inventory Visibility
Problem:
Without real-time visibility, businesses can’t make informed decisions about inventory levels, leading to stock imbalances.
Solution:
- Inventory Management Software:
Implement software that provides real-time inventory tracking and reporting. - Integrate Systems:
Ensure your inventory system integrates with other business systems like sales and accounting. - Cloud-Based Solutions:
Use cloud-based solutions for accessible, real-time data from anywhere.
6. Manual Processes
Problem:
Manual inventory processes are time-consuming and prone to errors, leading to inaccurate records and inefficiencies.
Solution:
- Automation:
Automate inventory tasks like data entry, stock counts, and reorder alerts with a WMS. - Barcode/RFID Systems:
Use barcodes or RFID tags for quick and accurate item tracking. - Train Staff:
Train employees on new technologies to ensure smooth transitions and efficient use.
7. Poor Demand Forecasting
Problem:
Inaccurate demand forecasting can lead to either excess inventory or stockouts, both of which are costly.
Solution:
- Data Analysis:
Use historical sales data and market trends to predict future demand. - Collaborate with Sales Team:
Get input from sales staff who are familiar with customer needs and market conditions. - Flexible Forecasting:
Regularly update forecasts based on actual sales and market changes.
8. Inventory Shrinkage
Problem:
Inventory shrinkage due to theft, damage, or misplacement can result in significant losses.
Solution:
- Security Measures:
Implement security cameras, locks, and employee background checks to reduce theft. - Regular Audits:
Conduct regular physical counts to identify and address shrinkage early. - Employee Training:
Train staff on proper handling and tracking procedures to minimize damage and misplacement.
9. Poor Supplier Management
Problem:
Unreliable suppliers can lead to delays, stockouts, and poor-quality inventory.
Solution:
- Supplier Evaluation:
Regularly evaluate suppliers based on delivery times, quality, and reliability. - Diversify Suppliers:
Don’t rely on a single supplier; have backups to ensure continuity. - Strong Relationships:
Build strong relationships with key suppliers to negotiate better terms and ensure reliability.
10. Ineffective Inventory Turnover
Problem:
Low inventory turnover means products stay in storage for too long, tying up capital and increasing holding costs.
Solution:
- Analyze Turnover Rates:
Regularly analyze inventory turnover rates and identify slow-moving items. - Promotions and Discounts:
Use promotions and discounts to move slow-moving inventory. - Just-In-Time (JIT) Inventory:
Adopt JIT inventory practices to reduce excess stock and increase turnover.
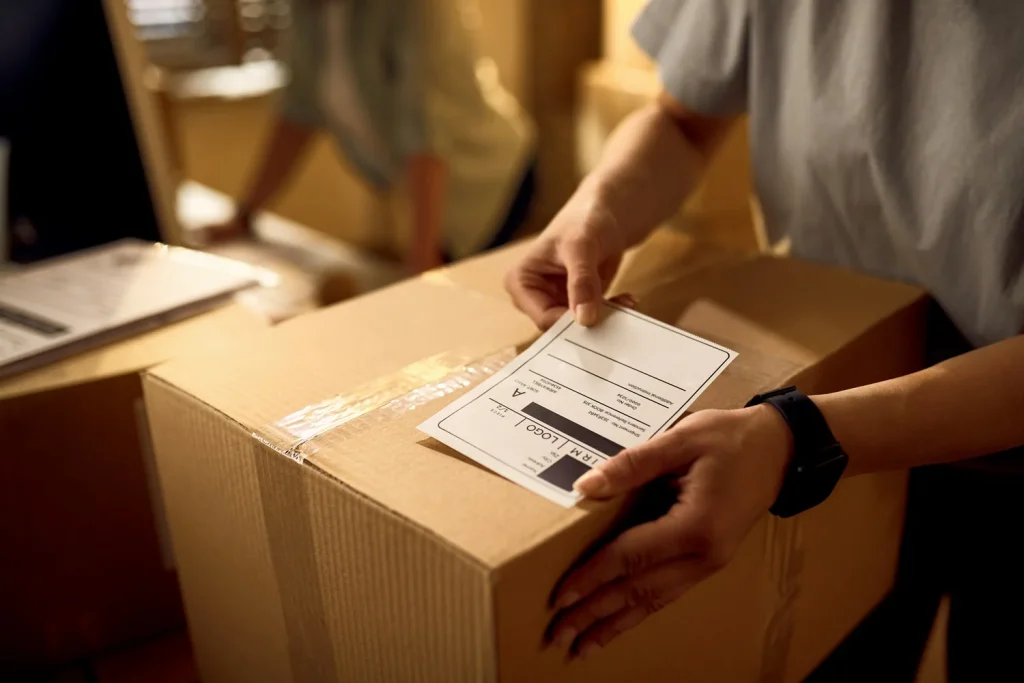
Conclusion
Effective inventory management is essential for the success of any business. By addressing these common problems with practical solutions, businesses can improve their inventory processes, reduce costs, and enhance customer satisfaction. Implementing systems like 8stock can make these tasks easier and more efficient. Remember, regular monitoring and adjustments are key to staying ahead of inventory challenges.
By focusing on these actionable tips, you can overcome common inventory management problems and keep your business running smoothly. Request for a demo today and Happy Managing!