Warehouse Shutdowns and the Festive Season: Navigating the Holiday Logistics Challenge
The festive season is a time for celebration, family gatherings, and well-earned rest for many. For warehouses, it often means temporary closures and reduced operational capacity. While this break is crucial for giving warehouse staff time to recharge, it also introduces logistical hurdles for businesses that rely on seamless inventory flow and on-time deliveries.
Planning for this period requires careful preparation and leveraging the right tools to minimize disruptions. This article explores the challenges posed by holiday closures and how Warehouse Management Systems (WMS) can be the solution businesses need.
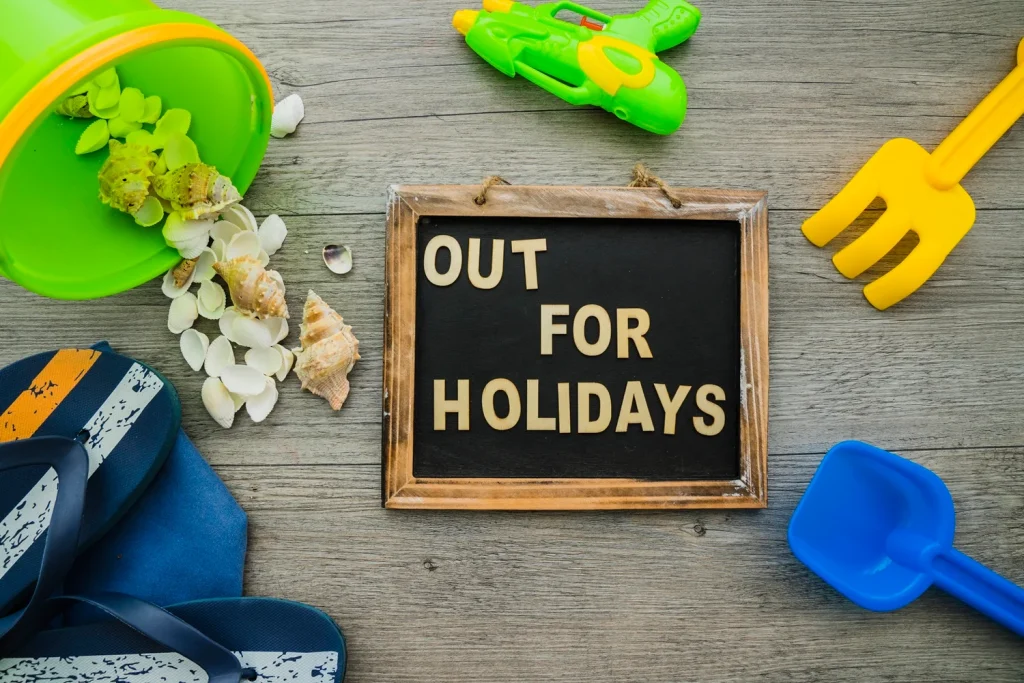
Why Warehouse Closures Matter During the Festive Season
Warehouse closures during the holidays can have ripple effects throughout the supply chain. The flow of goods slows or halts entirely, leaving businesses vulnerable to issues such as:
- Stockouts: Customers looking to make last-minute purchases might find items out of stock due to inadequate planning or unanticipated demand.
- Delayed Shipments: Orders placed close to the holiday period may not ship on time, leading to frustrated customers.
- Inventory Discrepancies: Without routine stock checks, there is a greater risk of discrepancies between physical inventory and system records.
- Security Risks: Unstaffed warehouses may face higher risks of theft or damage.
- Supply Chain Bottlenecks: Partners, such as suppliers and carriers, may also close for the holidays, compounding the logistical challenges.
The Role of a WMS in Navigating Holiday Logistics
Warehouse Management Systems are designed to optimize and streamline warehouse operations. During holiday closures, they become indispensable in helping businesses stay on top of their logistics. Here’s how:
1. Comprehensive Inventory Visibility
A WMS provides businesses with a detailed overview of their inventory levels before the shutdown. With this visibility:
- Businesses can forecast demand and adjust stock levels accordingly.
- Critical items can be identified and stocked up to prevent stockouts.
- Reordering can be automated, ensuring supplies are replenished in time for post-holiday operations.
2. Shipment Monitoring
WMS software integrates with carrier systems, allowing businesses to:
- Track shipments in transit, ensuring customers are informed of delivery timelines.
- Monitor potential delays caused by the holiday rush or carrier backlogs.
- Communicate updates proactively to customers, enhancing their experience.
3. Real-Time Reporting
During a shutdown, businesses need data to make informed decisions. WMS platforms offer:
- Reports on key metrics like order fulfillment rates and inventory turnover.
- Insights to optimize operations and reduce waste.
- An understanding of holiday performance trends, helping refine future strategies.
4. Security Alerts and Remote Monitoring
A cloud-based WMS can help monitor warehouse security remotely by:
- Sending alerts for unusual activity.
- Enabling businesses to review camera feeds or access logs if integrated with security systems.
- Minimizing downtime caused by theft or damage during closures.
Common Challenges Businesses Face During Holiday Closures
Even with the best tools in place, businesses must address several challenges to keep operations running smoothly:
1. Stockouts
Failing to stock enough inventory before the holiday season can lead to lost sales. To mitigate this:
- Use historical sales data to forecast demand.
- Prioritize high-demand items in your inventory planning.
2. Delayed Shipments
The rush to fulfill orders before a shutdown often strains shipping services. To avoid delays:
- Communicate cutoff dates for holiday shipping to customers.
- Partner with reliable carriers and maintain real-time visibility into shipment progress.
3. Inventory Discrepancies
Physical inventory counts are often put on hold during holiday closures. Without proper checks:
- Businesses may start the new year with inaccuracies in stock records.
- A post-holiday inventory audit can resolve this but may disrupt regular operations.
4. Supply Chain Disruptions
Holidays affect more than just your warehouse. Suppliers, manufacturers, and carriers may also experience closures. To prepare:
- Communicate early with partners about their holiday schedules.
- Build buffer stock for critical items.
5. Security Risks
Unstaffed warehouses can be targets for theft, vandalism, or environmental damage. Mitigation strategies include:
- Installing advanced security systems with remote monitoring capabilities.
- Scheduling periodic checks by trusted personnel during extended closures.
How an Efficient WMS Simplifies Holiday Logistics Management
An efficient cloud-based WMS can empowers businesses to tackle these challenges head-on. Such advanced features can provide comprehensive support before, during, and after the festive season.
1. Remote Inventory Management
Businesses can access inventory data anytime, anywhere. This feature ensures:
- Accurate stock assessments before closures.
- Continuous monitoring of inventory levels even when the warehouse is closed.
2. Real-Time Shipment Tracking
It can integrate seamlessly with carrier systems to provide real-time updates. This capability allows:
- Proactive communication with customers about their orders.
- Enhanced trust and loyalty through transparent delivery updates.
3. Automated Reporting
Able to generate detailed reports on performance metrics. These insights:
- Highlight areas for improvement.
- Help businesses make data-driven decisions for future holiday seasons.
4. Enhanced Security
With mobile capabilities, this allow businesses to manage warehouse security remotely. Features like digital access logs and integrations with security systems ensure warehouses remain safe during closures.
5. Seamless Post-Holiday Recovery
Reopening after the holidays can be chaotic, but an efficient WMS simplifies the process by:
- Automating routine tasks like stock audits.
- Providing a clear overview of pending orders and restocking needs.
- Streamlining operations so businesses can quickly return to peak efficiency.
Practical Tips for Navigating Holiday Logistics
To further ensure a smooth holiday period, here are some actionable tips:
- Plan Early: Start holiday preparations months in advance. Forecast demand, adjust stock levels, and communicate with partners about schedules.
- Set Customer Expectations: Clearly communicate holiday shipping deadlines, delays, and reopening schedules to customers.
- Leverage Technology: Invest in tools like 8stock to gain operational visibility and maintain control during closures.
- Secure the Warehouse: Implement robust security measures to protect assets during downtime.
- Prepare for Reopening: Develop a detailed plan for restarting operations, including restocking schedules and priority order fulfillment.
Conclusion
Holiday closures don’t have to mean logistical chaos. By understanding the challenges and leveraging tools like Warehouse Management Systems, businesses can maintain operational efficiency and customer satisfaction throughout the festive season. Such WMS stands out as a reliable ally, offering the features and support needed to tackle these challenges.
Don’t let the holidays disrupt your operations. Plan ahead, stay informed, and ensure a smooth transition into the new year with tools designed for success. Request a demo today to understand further!