Minimizing Warehouse Errors: Inventory Management Best Practices for 2024
In today’s fast-paced business landscape, the margin for error in warehouse operations is razor-thin. Mistakes in inventory management don’t just cost time and money—they can lead to dissatisfied customers, tarnished reputations, and operational inefficiencies that are hard to recover from. With 2024 underway, now is the perfect time to explore proven strategies and actionable insights to minimize warehouse errors and optimize your inventory management practices.
This guide will take you through the common types of warehouse errors, their impact, and the best practices to stay ahead of the curve.
Understanding the Cost of Warehouse Errors
Warehouse errors are not just a nuisance—they can cause cascading issues across the entire supply chain. Here’s how these errors typically manifest:
- Inventory Discrepancies
When stock levels are miscalculated, it results in either overstocking or stockouts. Overstocking ties up capital and increases storage costs, while stockouts can lead to lost sales and disappointed customers. - Picking and Packing Errors
Mistakes such as selecting the wrong item or incorrect quantities directly impact customer satisfaction. Orders with errors often need to be returned or replaced, driving up operational costs. - Shipping Mishaps
Errors in labeling, packaging, or inputting shipping addresses can lead to delays, damaged goods, or even lost shipments. Each mishap represents additional costs and harms customer trust.
The cumulative effect of these errors can damage your business’s reputation and profitability.
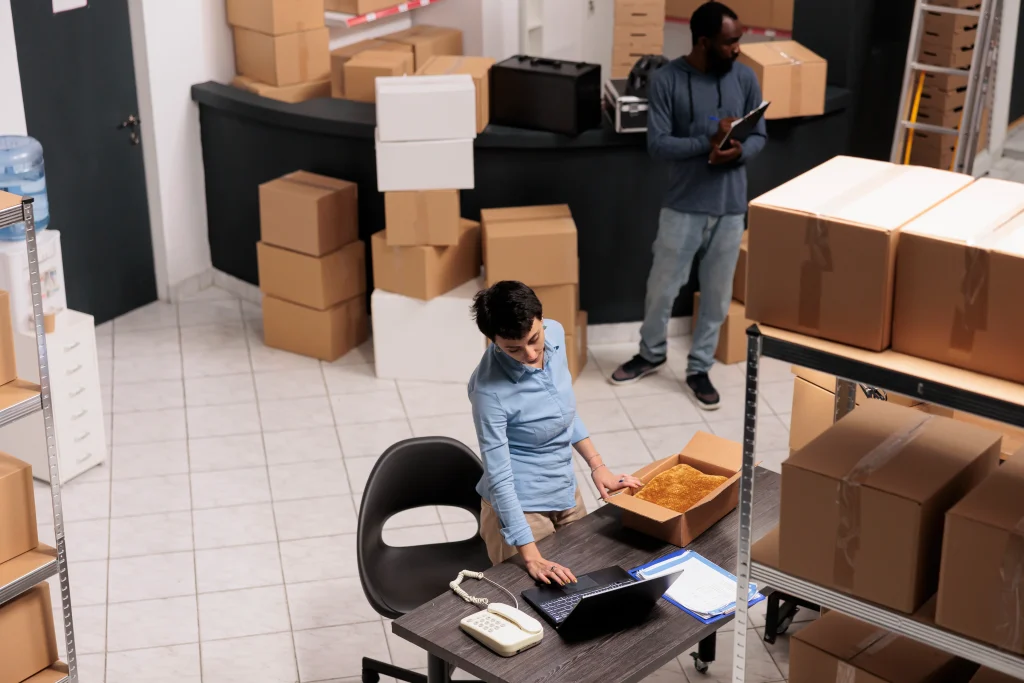
Inventory Management Best Practices for 2024
To minimize errors and keep your warehouse running like a well-oiled machine, consider implementing these cutting-edge practices:
1. Invest in a Robust Warehouse Management System (WMS)
A well-implemented Warehouse Management System (WMS) is your first line of defense against inventory errors. Modern WMS solutions offer:
- Real-Time Inventory Visibility: Track stock levels across locations without manual counting.
- Barcode Scanning and RFID Integration: Automate inventory updates to eliminate manual errors.
- Seamless Integration: Connect with ERP, e-commerce platforms, and supply chain software for better coordination.
- Actionable Analytics: Generate reports to identify bottlenecks and improve efficiency.
For instance, 8Stock, a comprehensive WMS, streamlines these processes, ensuring accuracy and efficiency while reducing human error.
2. Adopt Barcode Scanning and RFID Technology
Manual data entry is one of the leading causes of errors in inventory management. By adopting barcode scanning or Radio-Frequency Identification (RFID), you can:
- Enhance data accuracy by automating stock updates.
- Speed up inventory tracking and item retrieval.
- Reduce reliance on manual processes.
While barcodes are cost-effective for most warehouses, RFID is gaining traction for high-volume operations due to its ability to scan multiple items simultaneously.
3. Optimize Warehouse Layout
Your warehouse layout can make or break your operations. A well-organized space minimizes movement, reduces the risk of picking errors, and boosts overall productivity. Here’s how to optimize:
- Strategic Product Placement: Store high-demand items in easily accessible areas to reduce retrieval times.
- Clearly Defined Zones: Create dedicated zones for receiving, picking, packing, and shipping to streamline workflows.
- Ergonomic Storage Solutions: Use adjustable shelving or pallet racks to maximize space and minimize strain on workers.
4. Conduct Regular Cycle Counts
Instead of waiting for year-end stocktakes, conduct regular cycle counts. This involves counting a subset of inventory on a rotating schedule, which helps:
- Identify discrepancies early.
- Maintain real-time accuracy in stock levels.
- Build a habit of consistent record-keeping among staff.
Many warehouses adopt the ABC classification method for cycle counts, focusing on high-value (A), mid-value (B), and low-value (C) items in descending order of frequency.
5. Empower and Train Your Workforce
Technology alone cannot prevent errors—your workforce plays a crucial role. Well-trained employees are less likely to make mistakes and can adapt quickly to new processes. Focus on:
- Technology Training: Ensure workers understand how to use the WMS, barcode scanners, and other tools.
- Safety Protocols: Reduce the risk of accidents by emphasizing safe practices for handling equipment and inventory.
- Continuous Education: Offer refresher courses and opportunities to upskill.
6. Use Data Analytics for Smarter Decision-Making
Data-driven insights are a game-changer for inventory management. Use analytics to:
- Predict demand patterns and adjust inventory accordingly.
- Spot inefficiencies in picking routes or storage methods.
- Reduce waste by analyzing trends in returns and damages.
Advanced WMS tools like 8Stock provide dashboards and reports to help businesses make informed decisions that optimize warehouse performance.
7. Build Strong Supplier Relationships
Your suppliers are critical to your inventory’s success. Transparent and collaborative partnerships can help:
- Improve Lead Times: Get faster restocks to avoid stockouts.
- Increase Supply Chain Visibility: Share real-time updates on inventory movement.
- Enhance Communication: Resolve discrepancies quickly to maintain accuracy.
8. Embrace Automation and Robotics
Automation is no longer a luxury—it’s a necessity for minimizing errors in modern warehouses. Consider technologies like:
- Automated Guided Vehicles (AGVs): Transport goods within the warehouse without manual intervention.
- Robotic Picking Systems: Use robotic arms to pick and pack orders faster than human labor.
- Automated Storage and Retrieval Systems (AS/RS): Maximize vertical storage space and automate retrieval processes.
These technologies not only reduce errors but also enhance productivity and cut labor costs in the long run.
What to Expect in 2025 and Beyond
As warehouse management continues to evolve, here are some trends to watch:
- AI and Machine Learning Integration:
Predictive analytics powered by AI will revolutionize demand forecasting and stock replenishment. - Sustainability Initiatives:
More businesses will adopt eco-friendly practices, such as using renewable energy and reducing packaging waste. - Advanced Robotics:
Robots will take on more complex tasks like sorting, assembling, and even quality checks. - Enhanced Supply Chain Visibility:
Blockchain technology and IoT sensors will provide real-time tracking of inventory across the supply chain. - Focus on Employee Well-being:
Technology will assist workers rather than replace them, creating safer and less physically demanding environments.
Final Thoughts
By implementing these inventory management best practices and staying ahead of emerging trends, your warehouse can reduce costly errors, improve operational efficiency, and elevate customer satisfaction in 2024 and beyond.
Looking for a cutting-edge solution to streamline your warehouse operations? 8Stock is here to help. Request a demo today and discover how our WMS can transform your business.