Understanding Inventory Management and Its Objectives
Inventory management is an important process, akin to the backbone, of a warehouse. From the likes of overseeing and managing the purchasing to storage and use of such stocks. This includes from managing the raw materials to components and then the finished products, as well as warehousing and processing them. Effective inventory management ensures that a business has the right products in the right quantity for sale, without accumulating excess stock or missing out on sales due to stockouts.
What is Inventory Management?
This refers to the systematic approach of sourcing, storing, and selling stock—both raw materials and finished goods. It encompasses the entire flow of goods from the procurement stage to the final sale. Effective inventory management ensures that businesses maintain optimal stock levels, avoiding the pitfalls of overstocking and stockouts.
Overstocking is the excessive accumulation of stock beyond what is needed to meet customer demand, leading to increased holding costs and potential waste.
A stockout occurs when stock levels are insufficient to meet customer demand, resulting in missed sales opportunities and potential customer dissatisfaction.
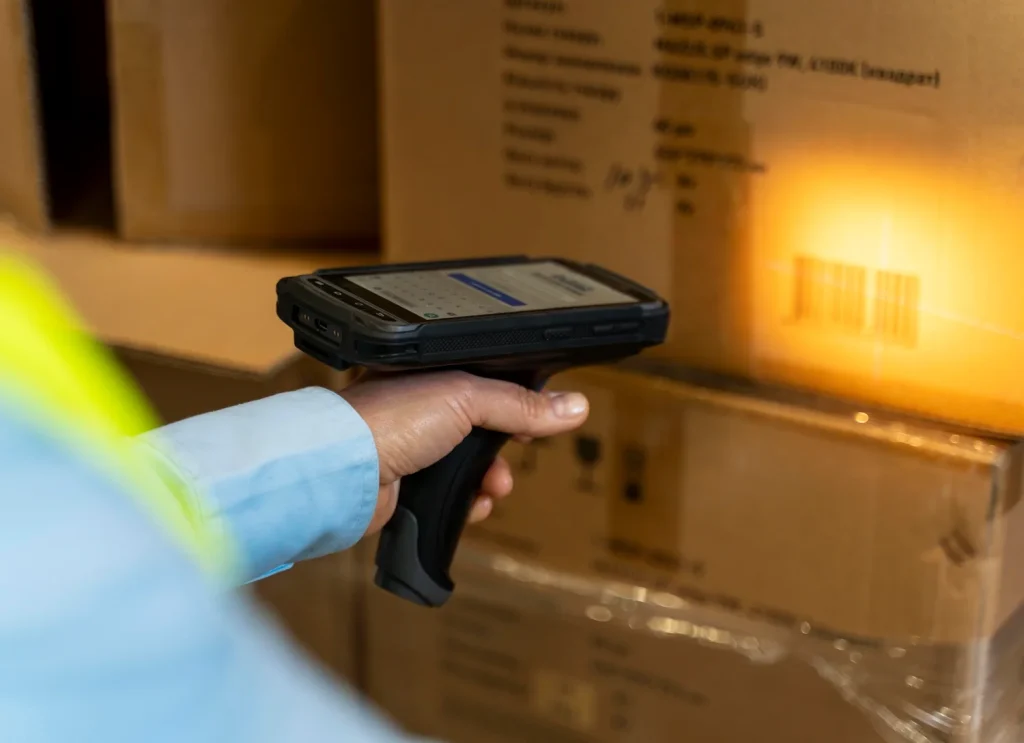
The Importance of Inventory Management
Why is inventory management so critical? Consider the following:
- Customer Satisfaction: Imagine a customer ready to purchase, only to find the product out of stock. Efficient inventory management prevents such scenarios, ensuring customers always find what they need.
- Cost Efficiency: Holding excess goods ties up capital and incurs storage costs. Conversely, stockouts can lead to lost sales and dissatisfied customers. Striking the right balance is key.
- Operational Efficiency: Smooth inventory management streamlines operations, from procurement to sales, reducing bottlenecks and enhancing productivity.
Objectives of Inventory Management
Now, let’s explore the core objectives:
1. Minimize Costs
Effective inventory management helps businesses minimize costs in several ways:
- Storage Costs: By keeping stock levels optimal, businesses reduce the need for excessive storage space, which can be costly.
- Insurance and Taxes: Lower stock levels mean reduced insurance premiums and taxes on stored goods.
- Inventory Turnover: High stock turnover indicates that products are selling quickly, reducing holding costs.
Example Data: According to a study by the National Retail Federation, retailers can reduce storage costs by up to 25% with efficient inventory management systems.
2. Ensure Product Availability
The primary goal is to ensure that products are available when customers need them. This involves:
- Demand Forecasting: Analyzing historical sales data to predict future demand accurately.
- Just-in-Time Inventory: Implementing systems where products arrive just in time for sale, reducing holding costs.
Example Data: Companies that implement just-in-time inventory systems can see a reduction in stockouts by up to 85%, according to the Journal of Business Logistics.
3. Optimize Stock Levels
Balancing stock levels is crucial:
- Avoid Overstocking: Excess stock ties up capital and incurs additional costs.
- Prevent Stockouts: Insufficient stock leads to missed sales opportunities and unhappy customers.
Example Data: A survey by the Institute of Supply Chain Management found that optimizing stock levels can increase profitability by up to 30%.
4. Improve Cash Flow
Efficient inventory management frees up capital that would otherwise be tied up in unsold stock:
- Quick Turnover: Selling goods quickly improves cash flow.
- Reduced Holding Costs: Lower stock levels reduce costs associated with storing unsold goods.
Example Data: Businesses can improve cash flow by 20-50% with effective inventory management, as per a report by the Financial Management Association.
5. Enhance Customer Satisfaction
Ensuring product availability and timely delivery enhances customer satisfaction and loyalty:
- Reliable Supply: Customers appreciate businesses that consistently meet their demands.
- Reduced Lead Times: Efficient systems shorten the time from order to delivery.
Example Data: Customer satisfaction scores can increase by up to 40% with effective inventory management, according to a study by the American Customer Satisfaction Index.
6. Streamline Operations
Efficient inventory management streamlines various business operations:
- Automated Systems: Modern inventory management systems automate routine tasks, reducing manual errors.
- Integration: Seamless integration with other business systems (e.g., accounting, sales) improves overall efficiency.
Example Data: Companies using automated systems report a 60% reduction in manual errors, according to a survey by the International Journal of Production Research.
7. Forecast Demand
Accurate demand forecasting is a critical component of inventory management:
- Historical Data Analysis: Using past sales data to predict future trends.
- Seasonal Adjustments: Accounting for seasonal variations in demand.
Example Data: Accurate demand forecasting can improve inventory turnover by up to 50%, according to the Journal of Operations Management.
8. Reduce Waste and Spoilage
Proper inventory management minimizes waste and spoilage, especially for perishable goods:
- First-In, First-Out (FIFO): Ensuring older stock is sold first to reduce spoilage.
- Regular Audits: Conducting regular inventory audits to identify and address issues promptly.
Example Data: Implementing FIFO can reduce spoilage by up to 70%, according to the Food and Agriculture Organization.
Techniques and Tools for Effective Inventory Management
1. Inventory Tracking Systems
Modern inventory tracking systems use barcode scanning, RFID technology, and real-time data analytics to provide accurate inventory counts and track movement.
2. Just-In-Time (JIT) Inventory
JIT inventory systems reduce holding costs by ordering stock only when needed. This requires accurate demand forecasting and strong supplier relationships.
3. ABC Analysis
ABC analysis categorizes products into three groups:
- A-items: High-value, low-quantity items requiring close monitoring.
- B-items: Moderate-value, moderate-quantity items.
- C-items: Low-value, high-quantity items that can be managed less frequently.
4. Economic Order Quantity (EOQ)
EOQ is a formula that determines the optimal order quantity to minimize total costs, including ordering and holding costs.
5. Safety Stock
Maintaining safety stock helps prevent stockouts during unexpected demand spikes or supply chain disruptions.
Real-World Examples
1. Amazon
Amazon’s advanced inventory management system ensures that products are available for quick shipment. They use sophisticated algorithms and robotics to manage inventory in their fulfillment centers, reducing costs and improving delivery times.
2. Walmart
Walmart’s inventory management system is renowned for its efficiency. They use data analytics and real-time inventory tracking to optimize stock levels, ensuring products are always available on their shelves.
3. Zara
Fashion retailer Zara uses a just-in-time inventory system to respond quickly to changing fashion trends. By producing limited quantities and frequently updating their inventory, they reduce waste and keep their offerings fresh.
Conclusion
Effective inventory management is crucial for any business dealing with physical products. It aims to balance stock levels, minimize costs, ensure product availability, and enhance customer satisfaction. Avoiding overstocking and stockouts is key to achieving these objectives. Tools like 8Stock can streamline inventory processes, providing accurate tracking and management solutions to help businesses optimize their inventory and improve overall efficiency.
Implementing modern inventory management techniques and tools can significantly improve a business’s bottom line. Whether you’re a small retailer or a large corporation, focusing on inventory management can lead to a more efficient, cost-effective, and customer-centric operation. Request for a demo today!